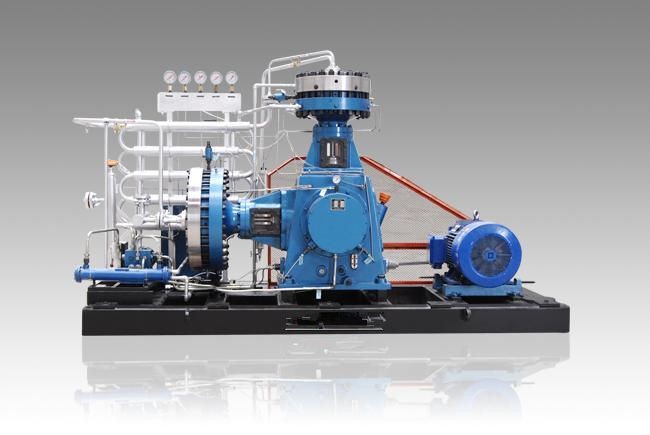
Diaphragm compressors are usually driven by an electric motor and driven by a belt (many current designs use direct-drive couplings due to associated safety requirements). The belt drives the flywheel mounted on the crankshaft to rotate, and the crank drives the connecting rod into reciprocating motion. The connecting rod and the crosshead are connected by a crosshead pin, and the crosshead reciprocates on the settlement segment.
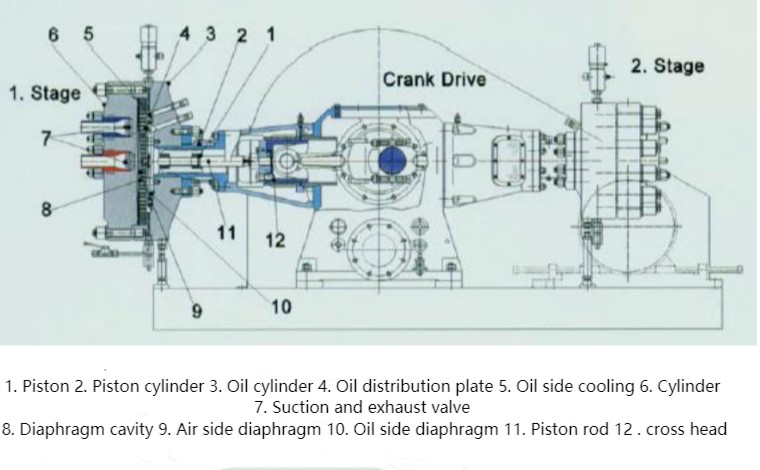
The hydraulic piston (piston rod) is mounted to the crosshead. The piston is sealed by piston rings and reciprocates in a hydraulic cylinder. Each movement of the piston generates a fixed volume of lubricating oil, thereby driving the diaphragm to reciprocate. The lubricating oil acts on the diaphragm, so it is actually the diaphragm compressed gas.
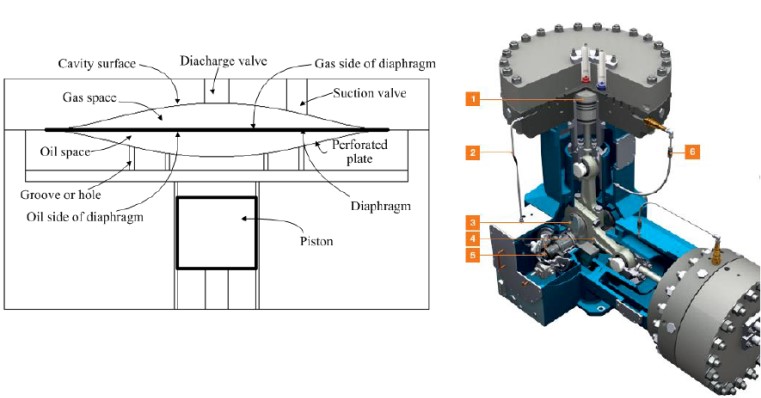
The main functions of hydraulic oil in diaphragm compressors are: lubricating moving parts; compressing gas; cooling. The circulation of lubricating oil starts from the crankcase, where the crankcase seat oil sump. The lubricating oil enters the inlet filter, and the lubricating oil is usually cooled by a water-cooled cooler. The lubricating oil then enters the mechanical oil pump and is filtered through the filter. Then the lubricating oil is divided into two ways, one way to lubricate the bearings, connecting rod small heads, etc., and the other way into the compensation pump, which is used to push the diaphragm movement.
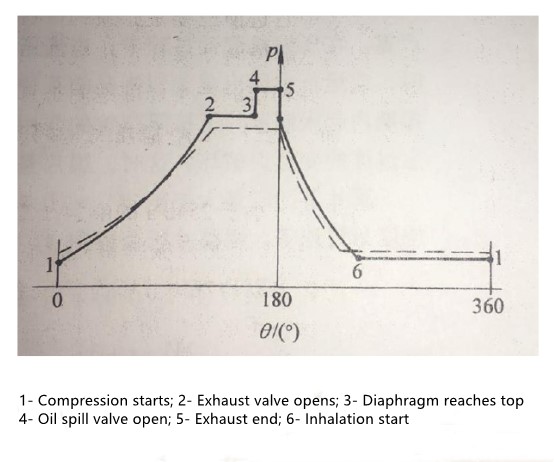
Post time: May-06-2022